격자구조소재 기술 활용 … 고효율 열관리 소재로 전기차 안전성 제고
소성가공 및 진공브레이징 기술 결합해 대량생산 가능
한국재료연구원(KIMS, 원장 이정환)의 스마트재료공정연구실 김상우 박사 연구팀이 ㈜하이박(대표 박재용), 한국자동차연구원과 함께 단위셀의 기하학적 형상설계로 기계적·열적 특성을 인위적으로 제어하는 3차원 금속격자구조소재 양산형 제조기술을 활용해 전기자동차용 알루미늄 배터리 열관리 시제품 개발에 성공했다고 24일 밝혔다.
격자구조소재는 특정 형상의 단위셀이 규칙적으로 배열되어 인위적인 다공구조를 형성시킨다. 단위셀의 소재와 형상, 크기, 배열의 설계를 통해 기계적 및 열적 특성을 제어할 수 있다. 경량성과 에너지 흡수성, 열전달 특성이 우수해 2개 이상의 기능을 동시에 갖춘 다기능 소재로 응용분야에 최적화된 맞춤형 설계가 가능하다.
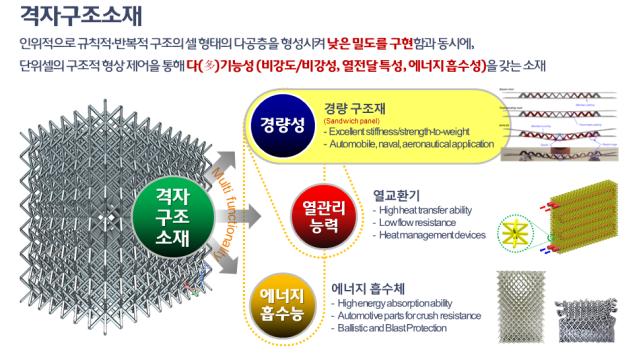
불규칙적인 다공구조나 체적소재에 비해 비강도와 비강성이 우수하기 때문에 항공기, 자동차, 선박 등 수송기기의 초경량 구조재료에 적용될 수 있으며, 외부의 충격 하중을 내부구조가 흡수하는 충격에너지 흡수능력도 우수해 내충격 재료, 방탄 및 방폭 재료로서의 잠재적 가능성도 함께 갖고 있다. 또한 개방형 격자구조는 표면적이 넓고 내부유동이 균일하여 전열특성이 우수하고 압력손실이 작아 열교환기, 히트싱크 등 다양한 열에너지 관리 장치에 활용 가능하다.
하지만 미국, 영국 등 일부 기술선진국에서 방위산업 분야를 제외하고는 민간분야에서 산업화가 쉽게 이루어지지 않고 있는데, 복잡한 내부 형상으로 인해 제조공정 비용이 높아지기 때문이다.
이에 재료연구원 연구팀은 금속소성가공기술로 단층 3차원 격자구조를 제작한 후 ㈜하이박에서 이를 다층으로 조립해 진공브레이징 접합을 통해 3차원 금속격자구조소재를 제조했다. 이러한 방식은 전통적인 금속가공 및 접합기술인 소성가공기술과 진공브레이징기술을 활용한 것으로, 별도의 설비 도입 없이 기존의 제조 인프라만으로 대량으로 생산할 수 있다.
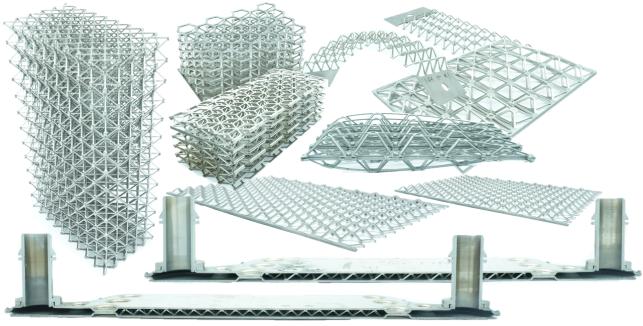
특히 고강성의 경량구조와 함께 에너지 흡수능력, 열관리 능력을 동시에 구현함으로써 경량·기능성 부품으로 적용이 가능해 미래 수송기기를 비롯한 다양한 산업분야에 확대 적용할 수 있다.
연구팀 관계자는 “금속격자구조소재가 적용된 전기차용 배터리 열관리 시제품 개발 및 특성평가를 통해 본 기술이 적용된 제품의 경량구조 특성과 방열 특성의 향상을 입증할 수 있었다”면서 “향후 다양한 산업분야의 고효율 다기능성 제품으로 활용하기 위한 초석을 다지는 계기가 될 것으로 기대된다”라고 밝혔다.
재료연구원 연구팀은 현재 8건의 금속격자구조소재 제조기술에 대한 국내외 특허를 보유하고 있다. 또한 ㈜하이박과의 기술이전 및 협력을 통해 향후 5년 내에 격자구조소재가 적용된 전기자동차용 배터리 열관리 제품의 사업화를 목표로 하고 있다. 사업화가 성공적으로 이루어질 경우, 연간 100억원 이상의 매출을 기대하고 있다.
한편 이번 연구는 산업통상자원부의 핵심소재원천기술개발사업(고강도 및 방열특성을 갖는 경량 다기능 Periodic Cellular Material 설계 및 제조기술 개발)의 지원을 받아 수행됐다.