윤의한 한국동기술연구조합 이사 /대창 기술연구소 소장
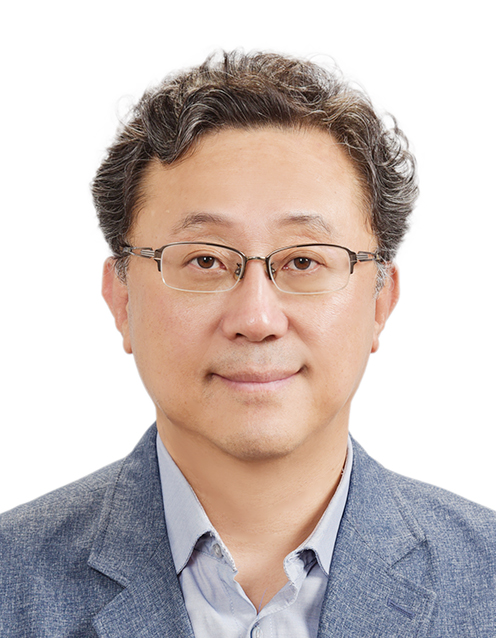
국립기술품질원(현 국가기술표준원)에서 홈닥터 제도로 담당하게 된 대창의 수직연주 빌렛 표면결함 해결을 시작으로 구리산업에 몸담은 지 30년이 되었다. 합금설계 전공자에게 구리합금의 소재개발은 흥미로운 연구과제였다.
첫 출근 날, 공장 견학에서, 산더미처럼 쌓여 있는 절삭 칩이 ‘우리의 쌀’이라는 회장님 말씀이 인상 깊었다. 스크랩을 재활용하는 환경친화적인 기업 이미지가 떠올랐다.
이를 세계 최고라는 브랜드명 BRASSONE과 친환경 소재라는 제품명 GEMBRASS로 표현했다. 구리산업의 8.5%인 황동봉은 구리와 아연에, 가공성을 위해 납이 2~3% 첨가된 단조황동과 쾌삭황동으로 크게 나뉜다. 그리고, 여러 가지 특성에 따라 새로운 소재들이 개발된다.
처음 개발한 소재는 내식황동으로, 배관의 누수와 계량기 오작동을 방지하여 환경부의 물관리 정책 추진에 공헌했다. 당시 사회적 이슈가 되었던 수자원 부족 문제를 해결할 수 있어 동강댐 건설 백지화에 기여했다.
두 번째는 방전가공용 황동선으로, 유럽에서 수입되던 소재를 국산화한 경우이다. 이때 스크랩 재활용 측면을 고려하여 첨가원소의 수와 양을 줄이면서도 원하는 특성을 얻게 되었다. 이는 향후 탄소중립에도 도움이 되었다.
범종 제작 업체인 종종사의 의뢰로 우리의 소리를 찾고자, 서양종의 실리콘 청동이 아닌, 주석 청동의 범종 소재를 개발했다. 조계사 스님들과의 만남과 에밀레 종의 설화에서 힌트를 얻어, 인을 첨가해서 건전한 주물을 만들 수 있었다. 현재 합천 해인사, 공주 마곡사, 양양 낙산사 등에 울림이 깊고 여운이 긴 한국의 종소리, K-Sound가 울려 퍼진다.
인은 인쇄회로기판의 회로를 구성하는 도금 공정에서도 중요하다. 당시 전량 수입에 의존하던 함인동볼은 전자업계의 큰 숙제였는데, 인 첨가량으로 도금 속도를 조절할 수 있었다. 일본업체의 임가공 제안과 가공비 덤핑을 이겨내어, 삼성전기를 시작으로 국산화 동볼로 대체 되었다. 최근 일본의 반도체 소재 수출규제를 생각하면 선행적 소부장 대책이었다. 더 나아가 정밀한 회로를 만들 때 사용되는 무산소동볼도 개발했다.
외식업이 확산되며, 불판의 수요가 급증하던 시기에, 납용출이 적은 소재 개발 요청이 있었다. 기존의 스크랩을 사용하지 않고, 무연황동 잉곳을 개발하여 매출량이 급격히 증가했다. 그러나, 다른 불판들의 납용출 문제가 이슈화 되면서, 환경친화적인 무연황동 잉곳도 함께 타격을 받은 뼈아픈 기억이 있다. 최근 KIST 전통르네상스지원단과 협력하며, K-Food를 뒷받침하는 유기 그릇, 수저 등의 변색 방지에 관심을 가지게 되었다.
한편, 납이 유럽에서 유해물질로 규제(RoHS)되면서, 구리합금 업계는 어려움을 겪고 있다. 일본은 실리콘 무연황동을 개발하여 세계시장을 선점했다. 입사 후 일본업체에서 3개월간 연수하며, 비스무스 무연황동을 개발하여 후발주자로 따라가고 있다. 이 합금들은 UNS 합금번호, ASTM 표준합금, KS 등록, US EPA 항균동 승인으로 이어졌다. 이후 무연쾌삭황동과 무연내식황동으로 환경마크와 녹색기술인증을 획득했다.
특히, 미국의 먹는 물 기준(NSF 61) 강화로, 수전금구용으로 널리 사용되는 내식 및 네이벌 황동을 내식계 및 네이벌계 무연황동으로 개량했다. 2022년 말, IWCC(국제구리가공협의회)도 유럽의 ‘무연황동 계획 및 로드맵’에서, 2036년까지 스크랩의 납함량 0.1% 이하를 목표로 내식계와 네이벌계 무연황동을 선정했다.
네이벌계 무연황동은 또한 양식 어망에 사용되기도 한다. LS 니코동제련(현 LS MnM)의 협조로 욕지도, 봉포항 등에 참치, 연어 등의 가두리가 설치되어 있다. 태풍을 이겨낸 황동 어망(GEMNET)은 유엔의 SDGs 중 식량 증대와 연안의 해저 오염방지에 기여한다.
또한, 극지방의 저온 해수에서도 높은 인성(toughness)이 필요했던 현대중공업의 요청으로 NiAl 청동을 개량했다. 전량 일본 수입의 원재료도 대체하여, 선박용으로 최대 110톤 중량의 프로펠러에 사용된다.
자동차 폐기물 규제(ELV)와 연계하여 싱크링과 동사판에 사용되는 고력계 무연황동도 개발했다. 타프피치동은 공정 개선으로 전기차 전장부품의 커넥터용에 적용된다. 특히 핸드폰 및 자율주행 차량의 각종 센서에 사용되는 카메라 렌즈 링 소재를 무연황동으로 대체하여 환경친화적인 전자제품(WEEE) 인식을 높이고 있다.
최근에는 연성(ductility)이 뛰어난 STS 관을 개발한 포스코의 철강솔루션연구소와 공동으로 브레이징용 용가재를 개발했다. 에어컨 공조기용 배관 부품과 함께 고부가가치가 기대된다. 다만, 수년 전 전자부품 패키징용 솔더링 소재의 대체재로 개발된 무연솔더가 상용화되지 못한 것은 아쉬움으로 남는다.
2023년 초, ICA(국제구리협회)는 ‘구리산업-탄소중립 로드맵’에서, 2050년까지 탄소배출 Net Zero를 선언했다. 구리산업의 탄소배출강도는 4.5 tCO2e/ton으로 철강 2.0, 알루미늄 9.2와 비교된다. 총 배출량은 1억 1,200만 톤으로 전세계의 0.2%에 불과하다. 유럽의 탄소국경조정제도(CBAM)는 철강, 알루미늄, 시멘트, 비료, 수소, 전력에 대해 이미 자료 제출을 요구했으며, 2026년부터 적용된다. 유럽 업계의 요구로 구리도 포함될 전망이다.
국내 제련업체인 LS MnM은 2022년부터 탄소중립 계획을 시작했으며, 반제품 생산업체도 어렵게 생각할 필요가 없다. 생산수율, 스크랩 재활용율, 용해로스, 에너지소비량, 폐열 등 관련 원가절감 활동 자체가 탄소중립에 기여하기 때문이다. 15년전 모스크바 철강대학과 수행한 용탕의 불순물 제거는 탄소중립에 필수적 기술이다. 여기에, 공급망 관련 Scope 3 부문을 더하면, ESG 경영과 결을 같이하게 된다.
탄소중립 로드맵은 풍력 터빈, 태양광 패널, 히트 펌프, 전기차 및 에너지 효율적인 장비와 같은 탈탄소화 기술을 수반한다. 기온 상승을 2℃ 이하로 목표한다면, 구리 수요는 2022년 2,500만 톤에서 2050년 5,000만 톤으로 증가가 예측된다. 1.5℃ 이하이면, 구리 수요는 5,700만 톤으로 증가하여, 구리산업에는 큰 비전으로 다가올 것이다.