세계 최고 기술력“월드베스트, 월드퍼스트를 찾아라”
포스코는 지난 반세기 가까운 시간 동안 우리나라 철강산업의 발전과 맥을 같이하며, 자원 한 톨 나지 않는 철강 불모지에서 세계를 선도하는 선도하는 기업으로 성장했다. 이러한 성장배경에는 포스코의 기술개발 노력이 뒷받침됐음은 주지의 사실이다.
정준양 회장은 “불황에서도 생존하려면 월드 베스트(World Best)와 월드 퍼스트(World First) 제품과 함께 월드 모스트(World Most) 제품을 개발해야 하며, 이와 더불어 필요한 것이 궁즉통 기술개발”이라면서 “원가·품질·생산성 부문 등에서 30% 이상의 획기적인 개선을 할 수 있는 기술로 후발 철강사들의 추격을 뿌리치려면 이 기술을 개발하고 표준화하는 것이 매우 중요하다”고 강조해 왔다.
포스코가 자랑하는 월드베스트, 월드퍼스트 제품과 기술에 대해 살펴보기로 하자.
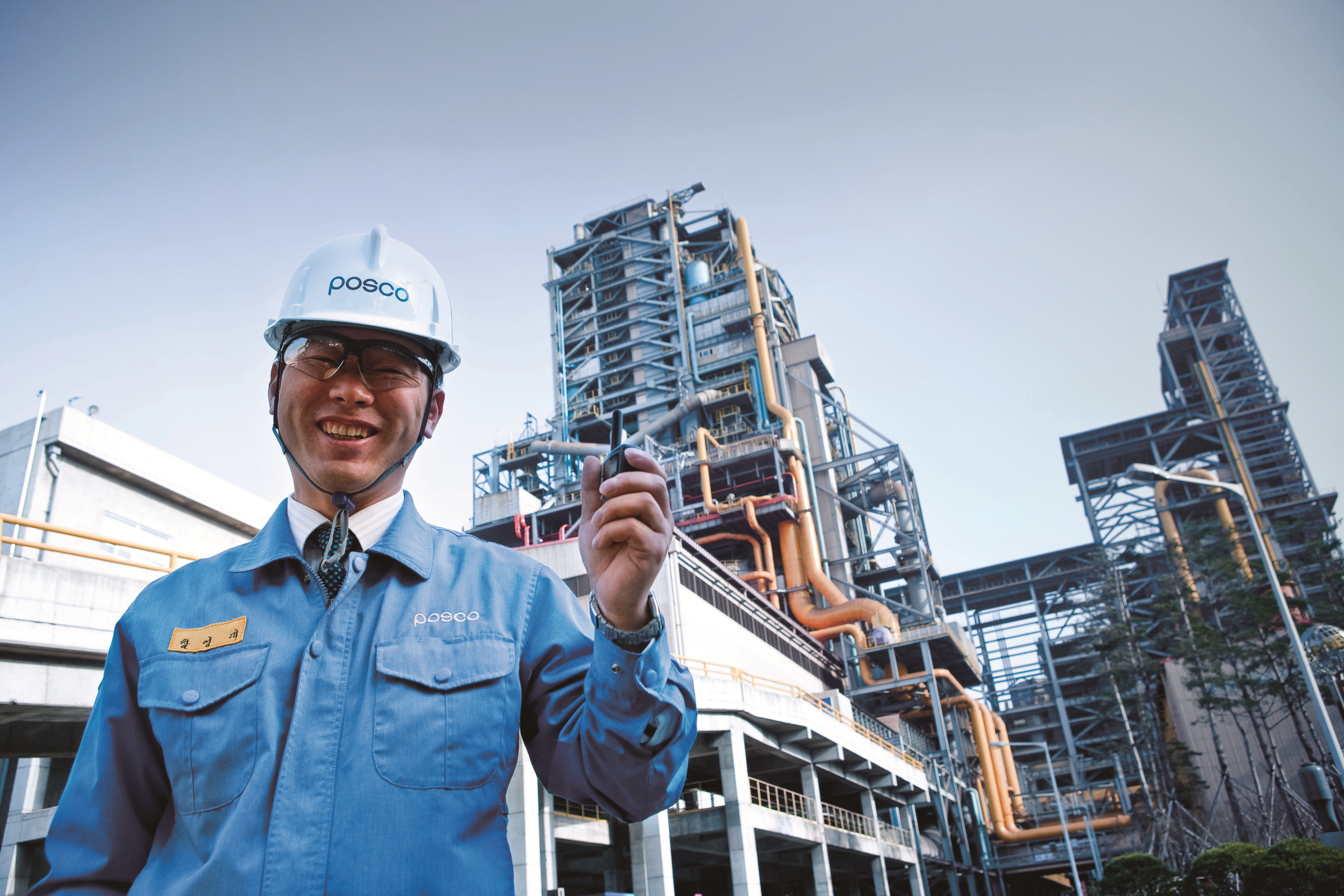
◆ 선강 분야
△ 세계 최대 고로 설계 및 시공기술
용광로의 경쟁력은 경제성 있는 저품위 원료를 다량 사용하면서 단위용적당 생산성을 향상시키는 것이다. 최근 상공정의 큰 투자 없이 후공정인 제강공정에 안정적으로 쇳물을 공급하고자 용광로가 대형화 되고 있는데 대형 용광로는 소형 용광로보다 용광로에 들어가 있는 장입물(철광석, 코크스)의 무게가 6,000톤 이상이 되기 때문에 기존 소형 용광로보다 3배 이상의 하중을 견디면서도 생산성을 높게 조업할 수 있도록 용광로를 설계, 시공하는 것이 핵심기술로 꼽힌다.
1973년 처음 불을 붙인 포항 1용광로의 내용적은 1,660㎥로 연간 생산량은 100만톤을 넘지 못했지만, 30년이 지난 지금 노체/노저 냉각설비 및 내화물 설계 기술 등 축적된 자체 설계기술을 바탕으로 광양 1용광로의 경우 내용적 6,000㎥, 연간생산량은 565만톤의 세계에서 가장 큰 용광로가 탄생하게 될 예정이다. 이는 포항 1용광로와 비교할 때 내용적은 3.6배, 생산량은 5.6배로 증가한 수준이며, 1개의 용광로가 예전의 용광로 3~4기를 대체한다는 의미가 있다.
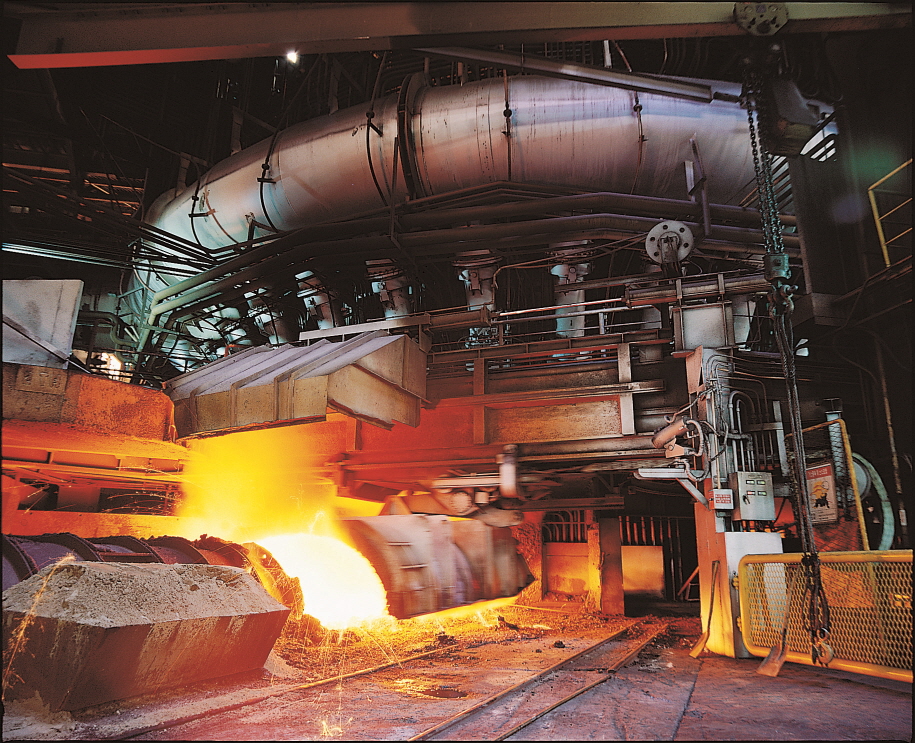
△ 차세대 혁신 제선공정인 파이넥스 기술의 진화
포스코는 용선 생산에 필요한 양질의 철광석과 석탄 고갈 및 가격 급등에 대비하여 기존의 용광로 공법을 대체할 파이넥스(FINEX) 공정개발을 1990년대부터 추진했다. 2003년 연산 60만톤 규모의 데모플랜트(Demo-plant)를 준공하였으며, 2007년에는 연산 150만톤 규모의 상업화 설비를 준공했다.
2008년에는 상업화 설비로 대형 고로에서 생산하는 용선의 톤당 석탄 사용비 730kg를 추월한 700kg 신기록을 수립하면서 프로세스 효율의 우수성을 입증했다. 이러한 150만톤 파이넥스의 기술적 자신감을 바탕으로 지난 2011년 6월에 세계 최초의 연산 200만톤 파이넥스 공장 건설을 시작해 2013년 12월에 준공을 앞두고 있다.
200만톤 파이넥스는 150만톤 설비와 같은 투자비로 생산성을 33% 향상시켜 설비 투자비 슬림화에 성공할 것으로 예상되고 있다. 또한 데모플랜트를 활용해 저품위 연원료를 다량사용할 수 있는 기술을 개발 중이며, 150만톤 상업화 설비로는 ‘코크스 제로(Coke Zero)’ 조업을 11개월 연속 이어가는데 성공했다. 이러한 기술들은 고로와의 차별성을 부여하여 향후 중국, 인도, 인도네시아 등 해외에 진출할 때 파이넥스 경쟁력을 확보하는데 기여를 할 것으로 판단된다.
△ 고속 연주~압연 직결공정 기술의 도약, CEM
포스코는 2009년 기존 미니밀 설비 합리화를 통해 슬래브를 생산하는 연주에서 열연코일을 생산하는 압연까지 단 한 번의 절단 공정 없이 생산(연연속 압연)이 가능한 새로운 공정 개발을 시작했다.
초기 누구도 경험해보지 못한 공정이라 시행착오 및 사고 발생으로 어려운 시기도 있었지만 포스코 특유의 근성과 끈기를 바탕으로 기술개발 노력을 지속한 결과, 2011년에는 현존하는 세계 최고의 연주기 생산속도 8.0m/min을 달성하였고, 2012년에는 안정적인 고속 생산 및 연주-압연 제어기술을 바탕으로 연연속 압연 제품 생산에 성공하여 박판 제품에 기존 고로밀 대비 길이/폭 방향 치수 및 재질 편차가 우수한 제품 생산 기술력을 확보했다.
포스코는 이에 멈추지 않고 연연속 압연 생산 공정의 제품 품질 및 강종 고급화를 통한 경쟁력 확보를 목적으로 제2단계 도약을 준비하고 있다.
◆ 압연 분야
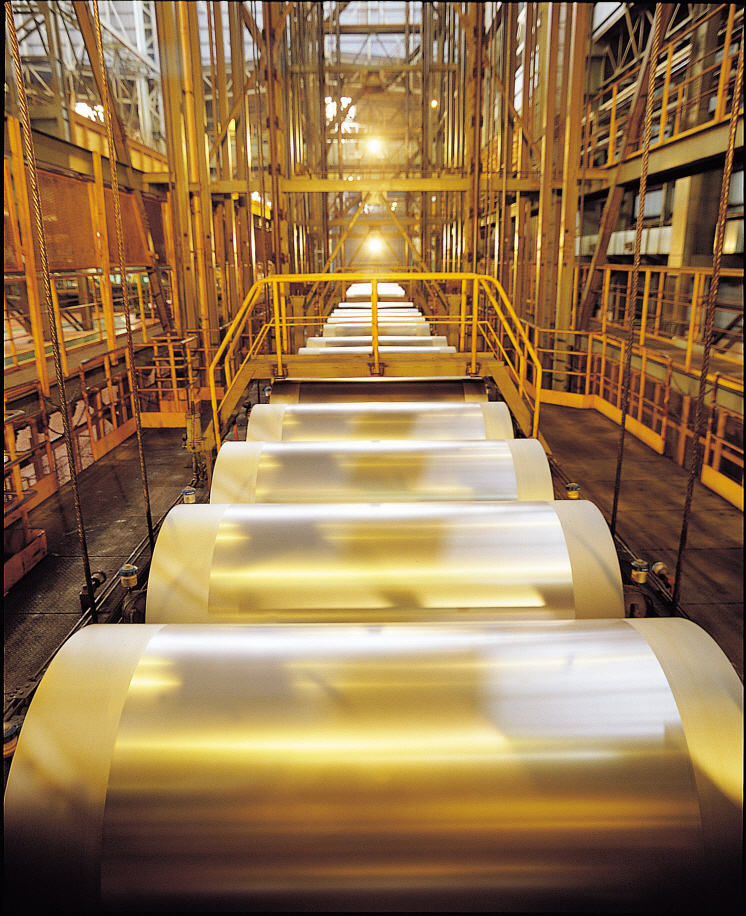
△ 나노석출물 활용 표면품질이 우수한 자동차강판(MAFE)
자동차외판용 개발된 MAFE강은 강판의 물성을 해치는 것으로 알려져 온 원소들을 잘 활용함으로써 합금첨가량을 줄일 뿐만 아니라 해로운 원소를 제거하고자 첨가하던 또 다른 원소를 첨가하지 않음으로써 제조원가를 대폭 줄이고 재질 편차 및 표면품질을 대폭 향상시킨 강종이다.
△ 내식성이 탁월한 고내식 합금도금강판(POSMAC)
이 제품은 기존에 사용되어온 아연도금에 비하여 약 10배 이상의 탁월한 내식성을 보유하고 있으며, 기존 고내식 합금도금으로 알려진 갈바륨(Zn-55%Al) 혹은 갈판(Zn-4.5%Al)에서 문제점으로 지적되어온 절단면에 노출된 철이 부식되지 않는 절단면 내식성이 탁월한 제품이다.
내식성과 함께 용접성, 도장성 및 가공성 등 모든 고객사가 요구하는 모든 특성을 기존 도금강판 대비 탁월하게 한 것이 특징이며 기존의 용융아연도금강판을 사용하여온 고객은 별도의 설비와 제조조건의 변경 없이 거의 유사한 조건으로 사용할 수 있다.
△ 세계 최초 전단방식에 의한 열연 연연속 압연기술
이 기술은 세계 최초의 전단 방식에 의한 고상 접합 연연속 압연기술로 일본 경쟁사의 레이저(Laser) 가열, 유도가열 접합 방식에 비해 좁은 공간에 설치할 수 있고 에너지 소모가 적으며 접합시간 단축에 의한 생산성 향상 및 접합부의 균일 품질 확보가 가능하다.
△ 장시간 PWHT 후 저온충격 보증용 60kg급 압력용기강(SA537-Cl2)
SA537-Cl2는 중ㆍ저온용 압력용기와 저장탱크 등에 사용되며 두께 100mm까지 요구되는 제품이다. 본 기술은 이 제품에 PWHT보증 성능을 확보, 타사 대비 시장진입에 경쟁우위를 선점한 기술이다.
* PWHT (Post-Weld Heat Treatment): 용접부 취화를 방지하고자 제품을 570℃~650℃ 온도로 가열하여 응력을 완화시키는 열처리
◆ STS 분야
△ 해양플랜트, 담수설비 및 발전설비용 슈퍼 스테인리스강 개발
포스코가 개발한 해양플랜트와 해수담수화설비 등에 사용되는 슈퍼 듀플렉스 강은 내식성 지수, PREN(=Cr+3.3[Mo+0.5W]+16N)값이 40 이상인 초내식 스테인리스강으로 매우 가혹한 부식환경에 사용된다. 이 밖에도 원자력발전소 복수기튜브 용도의 PREN 값이 45 이상인 슈퍼 오스테나이트 S32050과 Hyper Duplex강의 양산화로 산업설비용 초내식 소재로 공급될 전망이다.
△ 자동차 배기계용 고내열, 고내식 스테인리스강 개발
포스코에서는 종래보다 고온에서 사용 가능한 배기 매니폴드(Exhaust Manifold)용 POS429W1강을 개발하였다. 이 강은 기존의 내열 스테인리스강(STS444)에 비해 고온강도와 열피로특성이 30% 이상 우수하여 배기 매니폴드에 적용 시 작동온도를 높여 엔진효율을 크게 향상시킬 수 있다는 특징이 있다. 국내외 자동차 배기계 시장을 대상으로 고내열 스테인리스강의 시장확대 및 양산공급이 기대된다.
※ 배기 매니폴드(Exhaust Manifold) : 배기구에 연결되는 구성품으로서 연소된 배기가스를 모아 배기 파이프를 통해 배출하는 장치
◆ 자동차강판 분야
△ 전기자동차용 철강 차체 PBC-EV
포스코는 철강업체 최초로 전기자동차용 철강 차체(PBC-EV, POSCO Body Concept-Electric Vehicle)를 개발했다.
포스코는 제품 고부가가치화를 통한 수익창출과 주고객인 자동차 산업의 미래 경쟁력 강화를 지원하고자 2010년부터 본격적으로 전기자동차용 차체 개발에 나서 2년 만에 무게는 25% 가벼우면서 안전성은 2015년 적용되는 국제충돌안전규제 기준을 모두 충족하는 전기자동차용 차체 개발에 성공했다.
PBC-EV에는 일반 차체보다 초고강도강(UHSS, Ultra High Strengh Steel) 사용량을 40% 이상 늘리고, 열처리를 통해 강도를 강화하는 열간프레스성형(HPF, Hot Press Forming)과 가변롤을 사용해 초고강도강의 단면을 자유롭게 가공하는 가변롤성형(MDRF, Multi directional roll forming)과 같은 최첨단 공법을 적용했다.
이에 따라 PBC-EV는 제품의 제조부터 폐차 후 스크랩 회수까지 과정의 친환경성을 정량적으로 평가하는 전수명주기 평가(LCA, Life Cycle Assessment)측면에서도 기존 차량대비 약 50%의 온실가스 배출을 저감시킬 수 있다. 특히 고급강 사용량을 대폭 늘리면서도 기존 자동차와 유사한 제조방법을 적용해 생산라인을 변경할 필요가 없어 전기자동차 제조 증가비용을 최소화할 수 있게 했다.
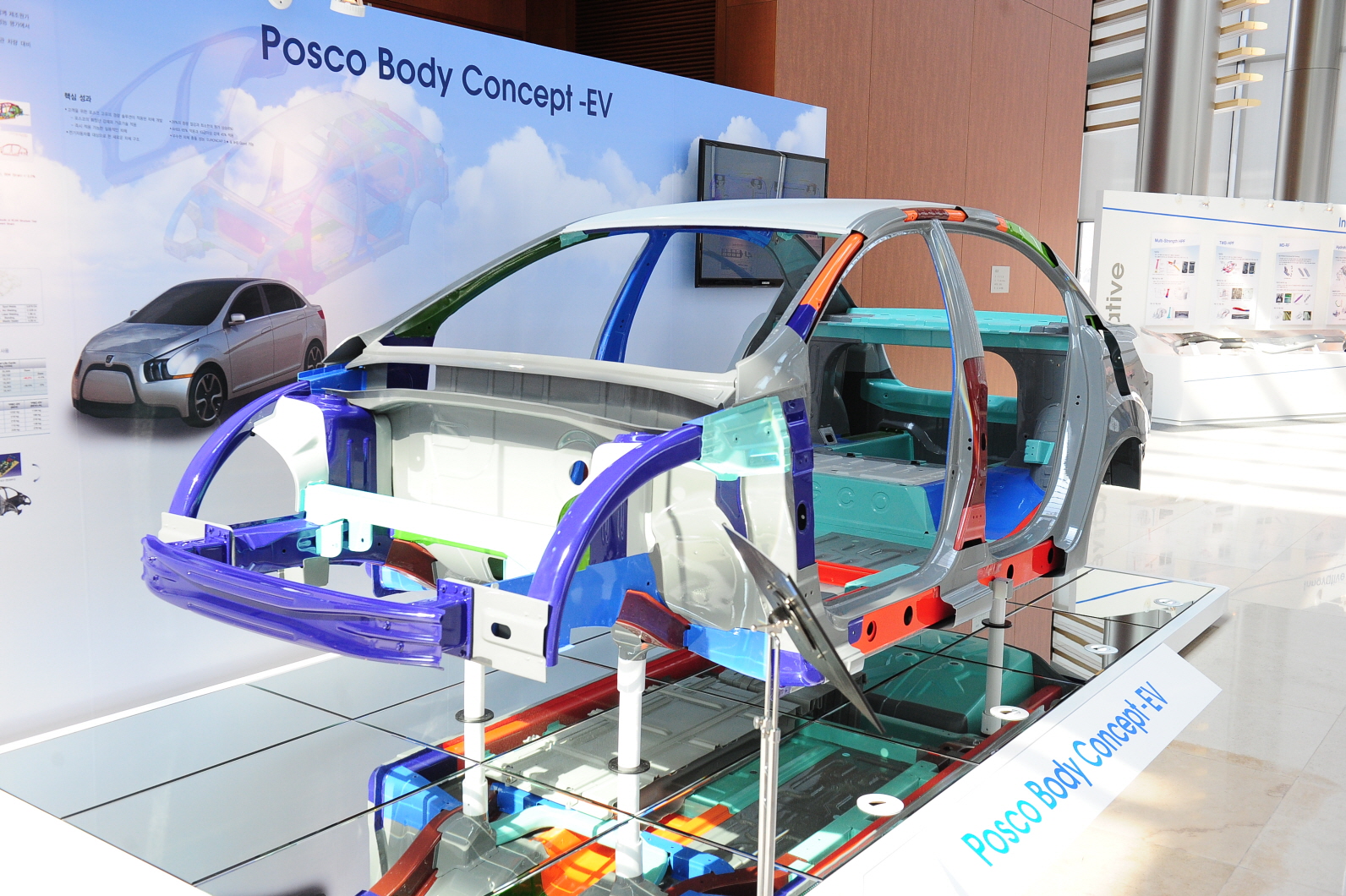
△ 첨단고강도강, 인장강도 490㎫급 AHSS 세계 최초 양산
포스코가 세계 철강사 최초로 인장강도 490㎫급 첨단고강도강(AHSS;Advanced High Strength Steel)을 자동차 외판재로 공급하기 위한 양산체제를 갖췄다. 1㎟당 최대 50㎏의 하중을 견디는 AHSS를 신형 싼타페 모델에 공급하며 국내 전 자동차사로 확대할 발판을 마련한 것이다. 포스코는 2007년 이 강종의 상업생산을 시작한 이래 EVI(Early Vendor Involvement)활동과 시장개척을 거듭해왔다.
AHSS는 일반적으로 사용되는 270~340㎫급 자동차 외판재보다 두께가 훨씬 얇아 차량 경량화가 가능하여 향후 자동차 외판재 시장에서 수요가 많이 늘어날 것으로 보인다.
현재 국내외 자동차사가 자동차 한 대에 적용하는 외판재 중 약 60%는 270㎫급이며 40%가 340㎫급이다. 이번 양산공급체제 구축으로 고객사는 340㎫급 강재를 사용하던 도어 부분에 490㎫급 강재를 적용할 수 있게 됐다. 미려한 표면 확보가 중요한 자동차 외판재는 인장강도가 강할수록 성형이 어렵지만 포스코는 이를 기술력으로 극복, 490㎫급 강재를 외판재로 양산 공급하는 성과를 거뒀다.
이번 AHSS의 외판재 적용에 따라 자동차사는 내구성 향상, 차량 경량화에 따른 연비향상 등으로 고객만족도가 크게 높아질 것으로 기대하고 있다. 특히 340㎫급 강재보다 약 1.5배의 하중을 견딜 수 있으며 강성이나 찍힘성도 매우 우수하고 보강재 사용이 불필요해 자동차사의 원가절감 효과도 크다. 고객사와 함께 금형설계, 프레스 기술 등을 공동개발해 외판에 적용한 결과, 차량도어에서 7% 무게를 감량하는 성과를 거뒀다.